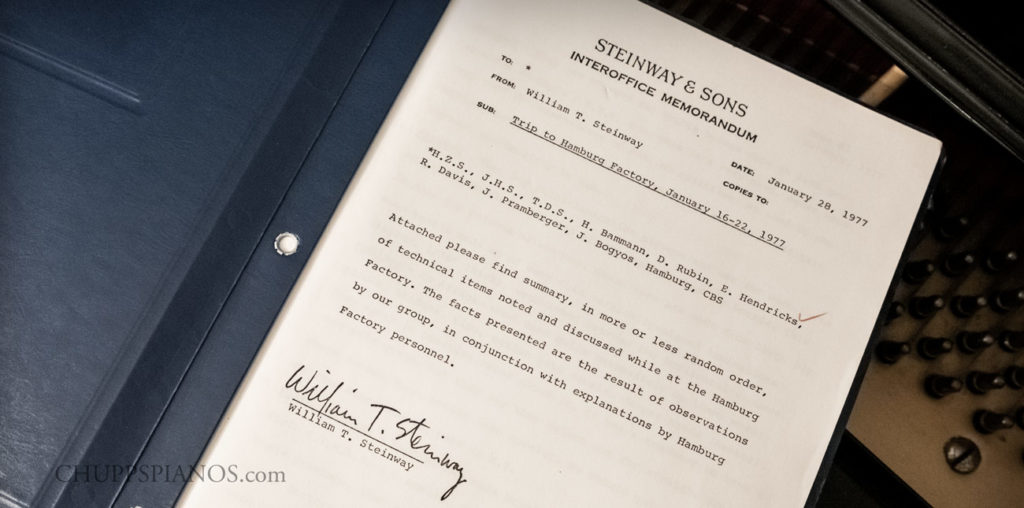
An Historic Glimpse Into the 70’s Hamburg Steinway Factory
One of the most unique parts of the Steinway story is the tale of two factories. Although with a name like Steinway (originally Steinweg), one could not be blamed for initially thinking that Steinway & Sons is a German company, transplanted to the United States. In fact, that is almost reversed. Founded in 1853 in the city of New York, Steinway & Sons was the brainchild of German immigrant Henry E. Steinway. Launching his new piano business into one of the most cutthroat and competitive businesses of his day, Henry and his offspring would quickly grow the company into one of the powerhouses of modern-day music. As demand increased in the United States, demand increased overseas as well. The decision was made to open a factory overseas and the Steinway name returned to Germany – the City of Hamburg, to be exact. In 1880, C.F. Theodore and William Steinway founded the Hamburg Steinway Factory. A wholly-owned venture, this new factory allowed them to avoid high import tariffs and allowed for easier distribution of their newly built pianos throughout the European market. Today, the Hamburg division continues to serve this purpose and most of the countries outside of North America are supplied with instruments crafted in Hamburg. Here in the United States, Hamburg Steinway pianos are often viewed as more ‘exotic’ and are known to possess a different tonal quality when compared to their New York factory brethren.
Like the ocean waves between them, the Hamburg and New York Steinway factories have drifted farther from and back closer to each other as the years have passed. In 1977, William T. Steinway (not to be confused with the William Steinway of the late 1800s) took a trip to the Hamburg Factory in order to report on the differences between the factories and their methods at that time. This historic summary titled ‘Trip to Hamburg Factory, January 16-22, 1977’ offers a unique snapshot of piano building during the late 20th century. Parts of this report have been reprinted below, specifically, the parts related to woods, plate work and action/tone regulation.
Woods
William noted that the Hamburg factory was fond of using boxwood for bridge caps. He noted it was a ‘…very hard, dense wood; very good for cleanliness of cut, no splitting.’ He also mentioned that the New York factory used to use boxwood and suggested they should investigate whether it was obtainable in the United States. African Bubinga was also in use – a wood that apparently, Hamburg was quite fond of and used extensively. According to William Steinway it was used for ‘wrest-planks, bridges, rims, action tube dowels, damper heads (Renner).’ Noted for its ‘wild grain’ he suggested experimentation with the wood at the New York Factory.
Hamburg keys were crafted from a lightweight spruce. William noted that ‘(it was) very clear and light in color. They say they have no breakage or warping problems.’ Buttons were constructed of basswood with an orange shellac finish. Kluge supplied many of the keyboards for Hamburg at that time, along with a company by the name of Bohn. Kluge was noted as having an interest in supplying keyboards for New York Steinways. This eventually came to pass and today, Kluge is a subsidiary of Steinway Musical Instruments.
The wrestplanks (pinblocks) were made from laminations of red beech, Bubinga and maple held together with a polyvinyl glue.
Grand piano rims were formed out of laminations of beech, maple, mahogany, and Bubinga. However, this varied on what was available in supply at that time. Other woods noted were the use of oak for some upright case work and grand piano keyframes. Pearwood veneers were also in use on keyblocks and the curve of the grand piano arms. This was due to the wood’s apparent ability to swell without cracking. It was mentioned that supply was low and other options were being explored.
Plate Work | Fit & Finish
It was noted that Hamburg did not take measurements when setting the V-rib (or bar) height. Leveled with a straightedge, approx. 1 mm of material would be removed to correct the shape. It was also mentioned that Hamburg at one point used the feller gauge method then in use in New York, but had discontinued its use due to front to back war-page of the plate throwing the gauge accuracy off. The V-rib itself was not hardened and historically was not done. At the time, they were experimenting with an attachable, hardened V-bar, a method seen today on some makes of pianos. It was also said that ‘…the plate iron that now get from electric furnaces is not as hard as what they used to get from cupola equipped foundries.’ Inspection included checking for breakage, wrestplank web thickness, and wrestplank straightness. They did not check for warpage at the time, as that would have required laying the plate onto a table. William said they found out if a plate was warped ‘too late just like us (at Plate Fit).” A plate with more than an 8mm thick wrestplank web was rejected. Plate finishing at the time was not done in house. Rather, the plates were ‘leveled and chipped, all holes drilled, then plates are Plate Fit and Bellied in raw state.’ After this, the plates were sent to an outside contractor for finishing. This contractor was the firm of Gunther. William noted that it was ’15 minutes away by car, run by a woman.’
William noted that after completion, the plate had ‘less damage to the finish than we have’ and any nicks or dings in the plate finish were touched up by brush after final tone inspection.
Action Work | Regulation & Voicing
Prior to regulation, the pianos in the Hamburg Factory were tuned ‘1/2 tone sharp’ and then tuned continually lower until reaching A440 to stabilize the piano prior to regulation. William noted that the ‘Hammers as they come from Renner seem to me to be excessively hard and excessively pointed in the treble.’ Compared to the soft felt of New York Steinway hammers that he was probably used to, it is easy to see where that opinion may have originated. The Tone Regulator he spoke to noted that they were generally pleased with the quality of hammers they were supplied with by Renner. If they felt the set of hammers they received were unworkable, they would very occasionally rip off the entire set and start over. The report notes that pianos were regulated in the following order;
- Action & Damper Regulating
- “What they call Action Regulation includes elements of our 2nd/3rd Finishing work and other elements we don’t include (e.g. their Action Regulators weigh and lead Keys, install backchecks, etc.). Action Regulators in Hamburg do two pianos a week.”
- Tone Regulating
- Their Tone Regulators do no action regulating work at all — only make tone and tune the piano themselves. They believe having the Tone Regulator tune his own pianos is an advantage, reasoning that if the piano goes out of tune while he is working on it he can bring it up right away without wasting any time looking around for a tuner. Their hammer filling method is similar to what Freddy Drasche teaches. They use a #60 grit open-coat sand paper file, thinner and more narrow that what Freddy likes.’
- Final Action & Damper Regulating
- Final Tone Regulating
- Action & Damper Inspection
- Tone Inspection
“This means in effect, that each piano is gone over three times for regulation and tone.”
Peppered throughout the report were references to a number of New York specific features and techniques. It was mentioned that they had sent the Hamburg Factory two uncompleted (case only) Model L Grands for their use and review as they were supposed to replace the Model O. Hamburg never did adopt the Model O and it would be New York who would eventually switchback, bringing the Model O back to the North American market in 2005. Renner action parts are continually mentioned throughout the report, a feature of Hamburg pianos only, as New York continued to build their own action parts. In 2019, Steinway Musical Instruments purchased the Renner company, putting that debate to rest. For more about the differences between New York and Hamburg Steinway Pianos, click here.
Interested in learning more about pianos? Keep on following our blog for continued posts and articles. For a list of our current inventory of restored Steinway and other grand pianos, click here.
*Documents are from the collection of the late Ed Hendricks, (Lyon & Healey, Steinway & Sons & Hendricks Pianos) courtesy of Bill Jenkins.
Chupp’s Piano Service – Restored Steinway & Sons Pianos – New Kawai Grand, Upright and Digital Pianos – Piano Restoration Services
Comments are closed