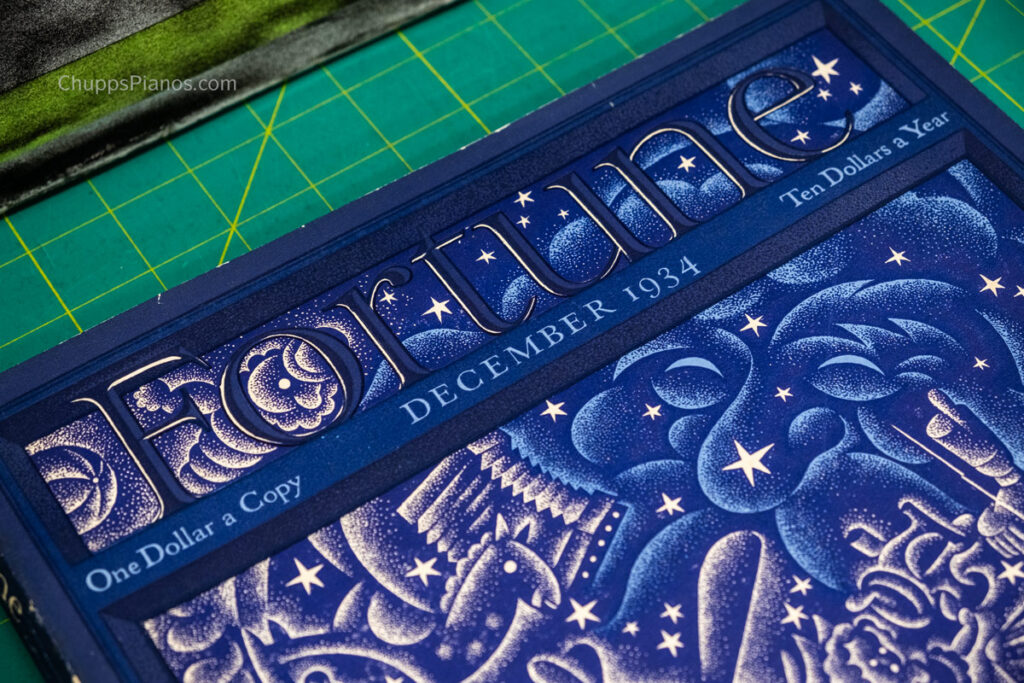
A peak into the mindset and organization of the historic New York Steinway Factory & It’s Famous Workers
In December of 1934, the Christmas Edition of Fortune Magazine was printed and delivered to subscribers. Retailing for One Dollar a Copy (or Ten Dollars a Year) the magazine during this time brought the hustle and bustle of the recovering industrial world to depression era readers across the North American continent. Among the companies highlighted was a company who’s legend was already firmly established – Steinway & Sons. Thanks to the generosity of Mr. John Kuehl our shop now has a copy of this magazine to add to our archive of piano documentation. We are pleased to share a few excerpts and photos from this historic profile!
INTRODUCTION: “The late Frederick Theodore Steinway was a grave, white-bearded patrician whose one great pride was his name and all it stood for. Frederick Theodore Steinway was a social somebody, but like all good Steinways he went to work, knew the insides of his pianos and what outsiders thought of them. A dealer called on him one day, told Frederick that he had traded too long on the name of Steinway, that to the profit of all concerned prices could be cut some $85 per piano. Frederick appeared convinced and the dealer quickly placed an order. “Just one flaw,” said Frederick. “Delivery will be delayed. It’ll take some time to remove the name Steinway from the keyboard.”
In the last eighty-one years The Name has crowned the keyboards of 280,000 pianos. Steinways, and Steinways alone, are played by Paderewski, Rachmaninoff, Gabrilowitsch, Horowitz, Hofmann, Artur Schnabel, and Myra Hess. Kreisler and Heifetz fiddle to Steinways. Arturo Toscanini has one for a shrine, on which he keeps his dearest mementos. A complete list would read like a musical peerage. It would speak of ghostly Franz Liszt and his glittering arpeggios, of Anton Rubinstein and untamed crescendos, of noisy Richard Wagner contented at last in the quiet of Wahnfried. Actual poets would be involved. The Steinways have purveyed pianos to the royal families of Britain, Norway, Sweden, Spain, Italy, Belgium, Turkey, Portugal, Persia. All pianos are numbered. No. 50,000 was an order from Baron Nathaniel von Rothschild in Vienna. No. 75,000 went by imperial warrant to Russia’s last Czarina. No. 100,000 would not be mentioned, really.
Ostensibly the White House favors no commercial concern. But it had to have a piano even in Theodore Roosevelt’s administration. In 1903 the $18,000 “gold grand” was installed in the East Room. Steinway is not allowed to advertise it. But 200,000 White House visitors see The Name there yearly.”
“STEINWAY WOOD…weathers two years outdoors before it is piled into this shed, here to season for as long again before it is taken into the factory, dried still more in patent humidity kilns. Each piece is hand-picked, sorted to kind, and labeled with its purchase date. The shed and the lumberyard outside hold 7,000,000 square feet of real lumber, valued at $1,500,000. Forty-two percent of a Steinway’s cost is in its wood, and much of the Steinway pride.” [SHOP NOTE: This rotating collection of old-growth lumber was key to the longevity and quality of historic Steinway and other golden era pianos.]
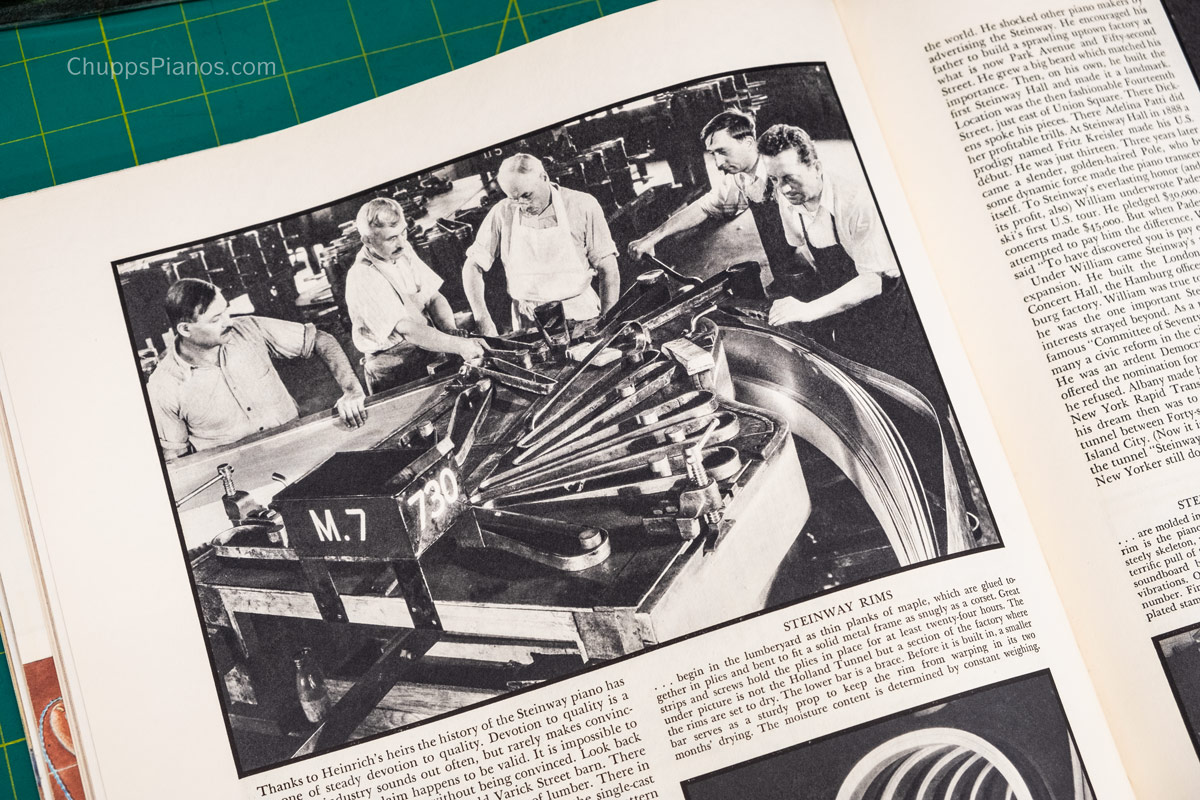
The Legendary Steinway Factory Rim Press – Circa 1934. This rim press was still in use when Dennis Chupp received training at the New York Factory.
“STEINWAY RIMS …begin in the lumberyard as thin planks of maple, which are glued together in piles and bent to fit a solid metal frame as snugly as a corset. Great strips and screws hold the piles in place for at least twenty-four hours. The upper picture is not the Holland Tunnel but a section of the factory where the rims are set to dry. The lower bar is a brace. Before it is built in, a smaller bar serves as a sturdy prop to keep the rim from warping in its two months’ drying. The moisture content is determined by constant weighing.”
“STEINWAY PLATES …are molded in the Steinways’ own foundry. If the rim is the piano’s flesh and blood, the plate is the steel backbone, strong enough to take the terrific pull of the strings, yet thin enough so that the soundboard beneath can reflect the most sensitive vibrations. On each plate is stamped a date and a number. Final process is the bronzing and the gold-plated stamp of “Steinway & Sons.” [SHOP NOTE: Steinway plates are no longer case in New York, and are now cast at O.S. Kelly Co. in Springfield, Ohio. This company was purchased by Steinway Musical Instruments/Conn-Selmer in 1999.]
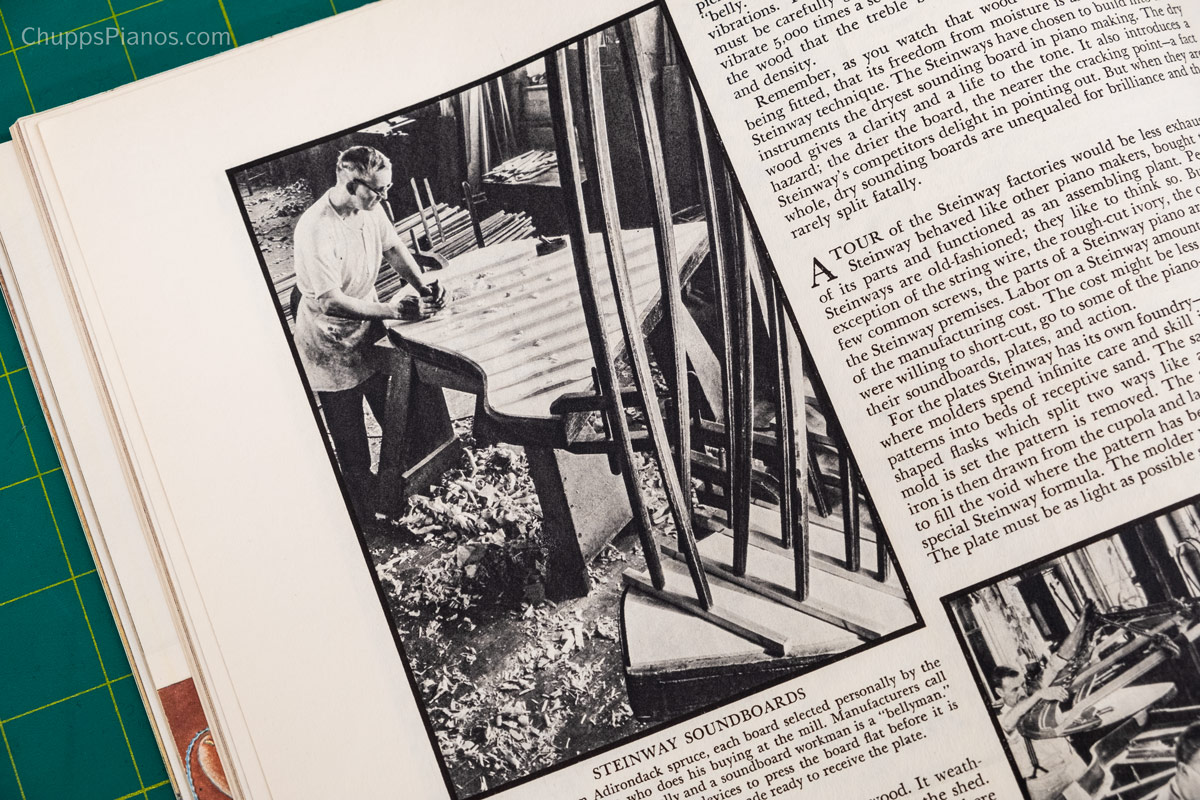
A Steinway ‘bellyman’ working on the supporting ribs of a solid spruce soundboard. Photography by Margaret Bourke White for Fortune Magazine in 1934.
“STEINWAY SOUNDBOARDS…are made from Adirondack spruce, each board selected personally by the Steinway lumber expert who does his buying at the mill. Manufacturers call the soundboard the piano’s belly and a soundboard workman is a “bellyman.” The ribs on the right are factory devices to press the board flat before it is put to bed in the framework of the rim, made ready to receive the plate.”
“THE KEYS OF A PIANO… are much longer than you would guess by seeing a finished keyboard. The ivory key tops (one of Steinway’s few importations) have been glued to a solid board before band saws make the final cutting. The hidden ends of the keys run on into the maze of parts that is known as the piano’s action.” [SHOP NOTE: Steinway New York would continue to utilize ivory as their primary key top material until the mid 1950s.]
Additional Quotes:
“It was because of Charles that The Name changed from Steinweg to Steinway and the U.S. gained the honor of producing the world’s finest piano. What the Steinwegs would have accomplished in Germany is unpredictable. They had a tidy
business there, sound capital, a well-working factory. But up popped the Revolution of 1848 and slump went trade. Theodor, we have seen, was a worker. But Charles was twenty, handsome, headstrong, obsessed by the preachments of Benjamin Franklin and Thomas Jefferson. He talked a little too much about liberty and the authorities got after him. So he escaped to New York, got a job in a furniture shop, and started writing home. Not so much about pianos but about furniture, which every- body wanted. And perhaps in time there would be a future for pianos…”
“Devotion to quality is a phrase that industry sounds out often, but rarely makes convincing. The Steinways’ claim happens to be valid. It is impossible to consider the family’s history without being convinced.”
“A TOUR of the Steinway factories would be less exhausting if Steinway behaved like other piano makers, bought the bulk of its parts and functioned as an assembling plant. Perhaps the Steinways are old-fashioned; they like to think so. But with the exception of the string wire, the rough-cut ivory, the castors, and a few common screws, the parts of a Steinway piano are all made on the Steinway premises. Labor on a Steinway amounts to 52 per cent of the manufacturing cost. The cost might be less if the Steinways were willing to short-cut, go to some of the piano-supply houses for their soundboards, plates, and action.”
About Us: Since 1975, Chupp’s Piano Service, Inc. has been specializing in the full rebuilding and restoration of vintage grand pianos. Located in the heart of Northern Indiana, our work has grown to become the preferred choice of numerous concert venues, institutions, and pianists around the world. We understand the nuances and exacting precision needed to ensure a piano that is truly tailor-made for your tastes and playing preferences. We are proud to continue the historic tradition of fine craftsmanship and dedication to quality that families like the Steinways have pioneered.
Founded by Master Piano Technician Dennis Chupp, our team is made up of top piano specialists. Our work continues to be executed with a focus on the piano as a musical instrument foremost in mind. From pianos destined for a loving home to those crated for the concert stage, we strive to complete the finest work possible. For more information about our craft, feel free to get in touch with us via email or phone. If you are seeking a piano that has already been restored, our facility in New Paris, Indiana features one of the largest selections of fully restored Steinway & Sons pianos anywhere in the Midwest. Click to view our selection of premium restored Steinway & Sons Grands, Pre-Owned Yamaha, and many other fine pianos.
ARCHIVES: A Look into the Hamburg Steinway Factory
Comments are closed